A Good Practice Guide to Placing Sensors in Machines
The following sections will present best practices in the positioning of Dynamox vibration and temperature sensors for typical industrial machinery, such as motors, pumps, compressors, exhaust fans, etc.
The objective of the guide is to assist the user in choosing a suitable location for installation of the sensors, helping to obtain reliable and quality data that allows an effective predictive analysis.
The guide will also indicate which sensor best applies to each machine, focusing on the following models:
DynaLogger HF + : Triaxial temperature and vibration monitoring with a maximum frequency of 13000 Hz, performing telemetry and spectral analysis
DynaLogger TcAs : Triaxial vibration and temperature monitoring with frequency up to 2500 Hz, performing telemetry and spectral analysis
DynaLogger TcAg : Triaxial vibration and temperature monitoring with a maximum frequency of 2500 Hz.
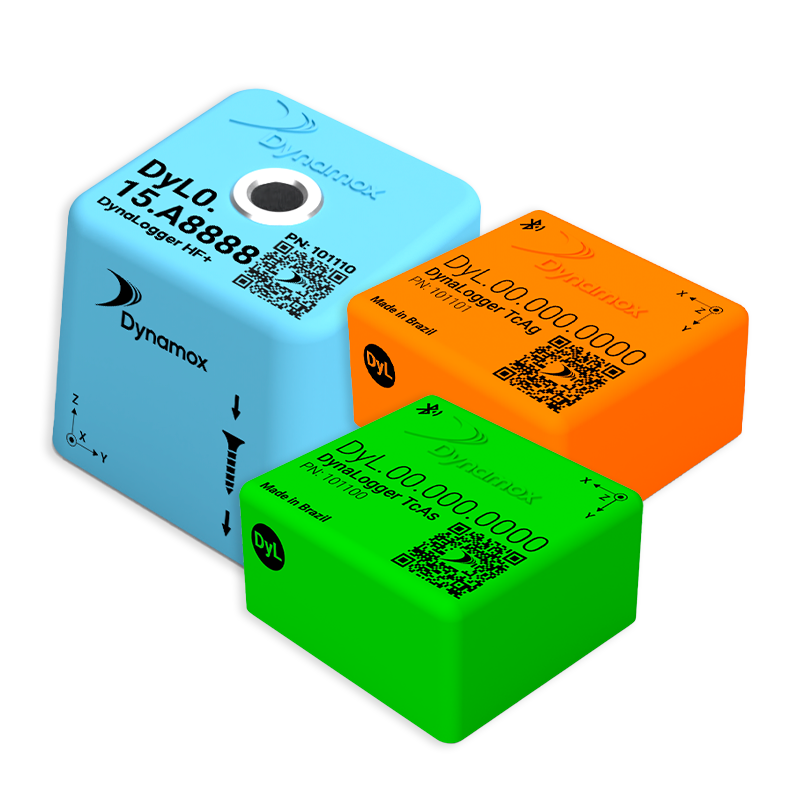
NOTE: The information contained in these sections are only recommendations and should not be taken as positioning rules.