Electric Motors
How to monitor electric motors with the DynaPredict Solution:
Electric motors are responsible for the operation of the majority of industrial equipment to generate movement. Failures in this component may cause a halt in production as well as accidents.
Monitoring operational conditions is an important activity in the search for reliability of these assets.
Dynamox’s sensors allow for the online monitoring of parameters such as vibration and temperature which allow for the identification of potential defects and planned interventions, thereby reducing production downtime and increasing the efficiency of the production process as a whole.
Regarding the position of sensors at an electric motor, it is recommended the monitoring be done either from the drive end (DE) or non-drive end (NDE) as shown in the image below.
OBS: the NDE spot may offer certain challenges to the sensor mounting, because of the protective cover. If necessary, consider drilling a hole or cutting a notch in the cover to allow access to a rigid mounting location. Never install sensors on the motor terminal or cooling fins, which are parts that emit high levels of vibration and make fault analysis difficult.
Regarding this equipment, two types of sensors can be used:
- DynaLogger HF+. A sensor with a maximum frequency of 1300 Hz. This sensor is recommended for motors coupled to equipment of most importance. Due to its high frequency range, it is possible to identify early stage bearing or lubrication defects, as well as faults in the rotation frequency of the machine, such as with the TcAs.
- DynaLogger TcAs . A Sensor with a maximum frequency around 2500Hz, which is recommended for low to medium criticality machines that do not present a history of bearing or lubrication related failures, since these defects may usually appear at higher frequencies. These sensors allow for the detection of faults in the rotational frequency of the machine, such as unbalance, misalignment, looseness and others. Besides, this sensor can be useful to detect bearing defects in the later stage.
For the DynaLogger mounting, there are two main alternatives: studor adhesive mounting. See more details here under item 4.
Regarding defects, the following root causes related to the machine problems, in terms of the axis and its characteristic frequencies, are indicated below:
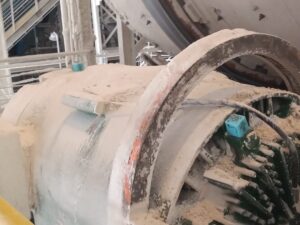
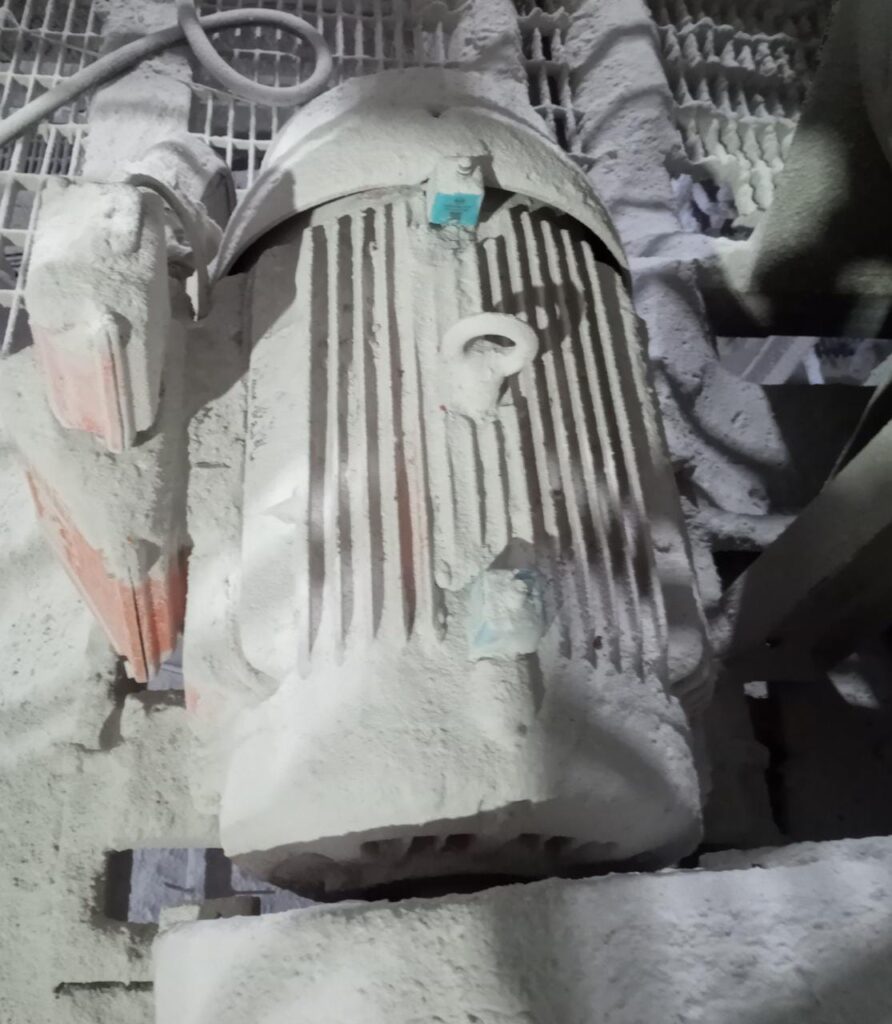
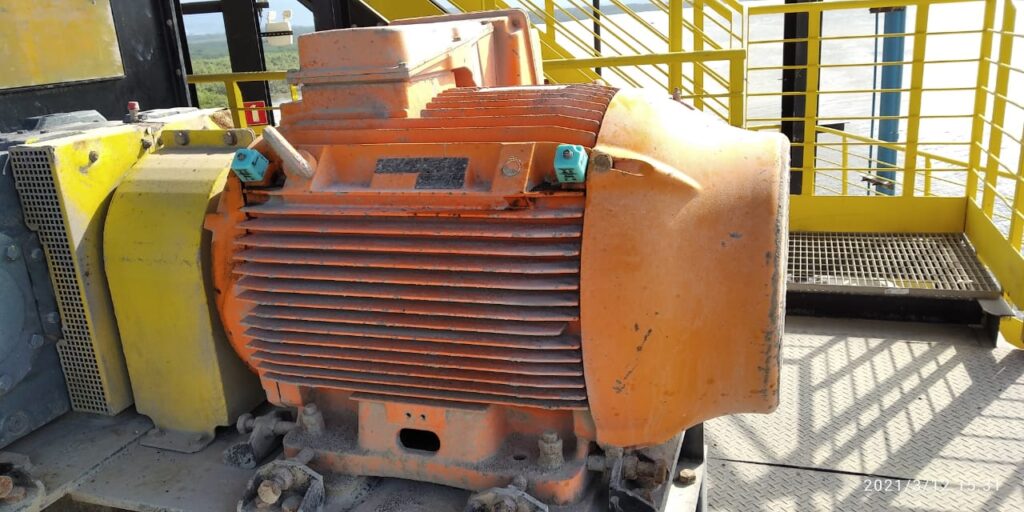